Automated steel processing
It is technically possible to automate steel machining processes at a high level and thus reduce manual interventions in the process. Efficiency, lack of professionals and cost price reduction are often the underlying reasons for automated processes.
In addition to the automatic operations themselves, it once began with the automatic transfer of structural steel (2 - 30 metres long) over roller conveyors to and from an operation. It is now possible to transport structural steel to and from various processes (blasting, sawing, drilling, coping, marking, etc.) without manual intervention, whereby, for example, sawing remains or short pieces are automatically removed.
As a result, structural steel dimensional deviations as a result of automation are becoming increasingly critical to the productivity of automated steel machining processes. The higher the degree of automation, the more accurate the starting material usually has to be for a process without disturbances.
Unplanned stops and therefore loss
Profiles with significant dimensional deviations do not so much cause malfunctions in the machine tools themselves, but rather in and on the conveyor systems to and from the machines.
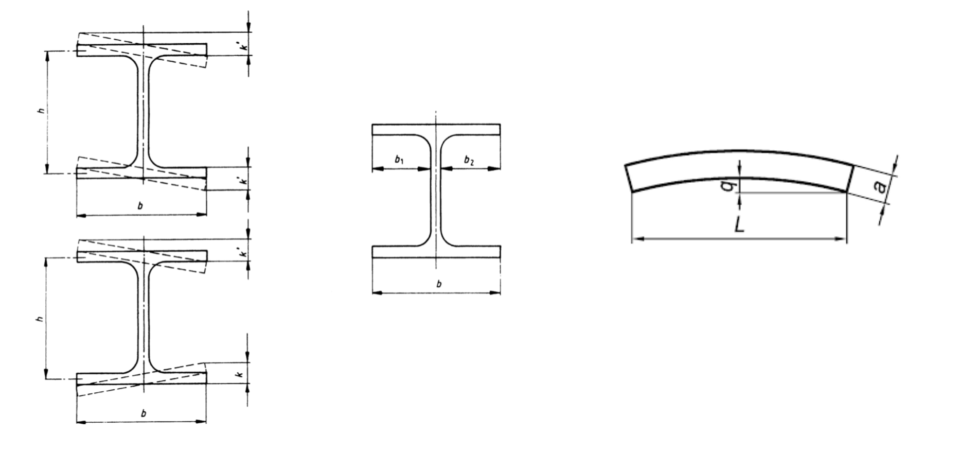
Material dimensional tolerances and tolerances on length
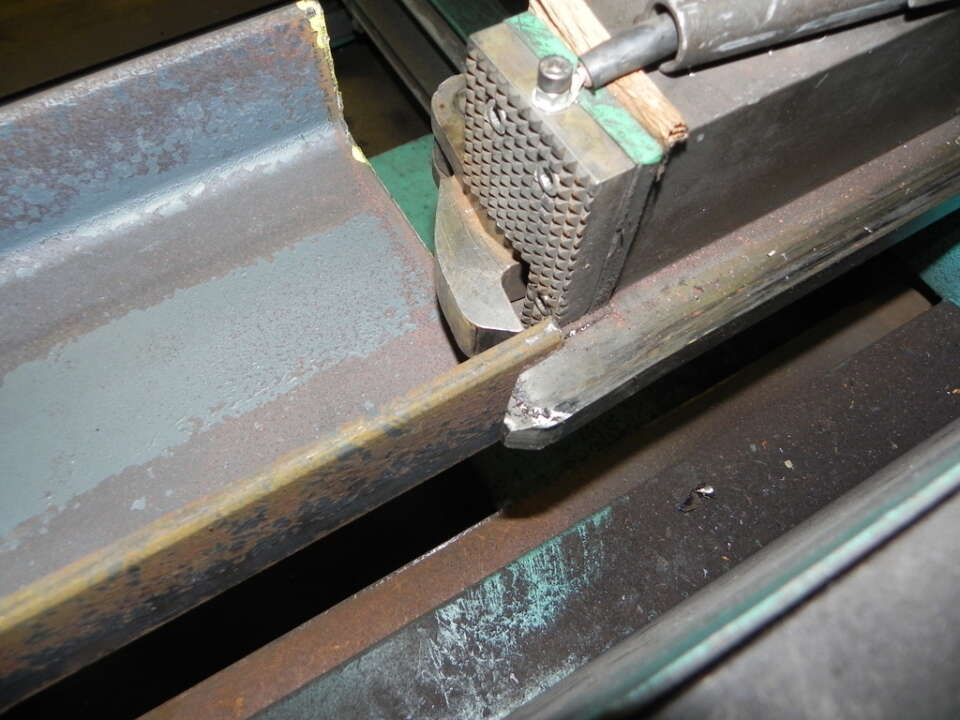
Example of gripper system
A saw / drill installation equipped with a so-called gripper system to grip the beam and ensure the length measurement, will not or with difficulty find and gripping sections with a considerable dimensional deviation. Manual intervention is often required to restore the interrupted automatic system.
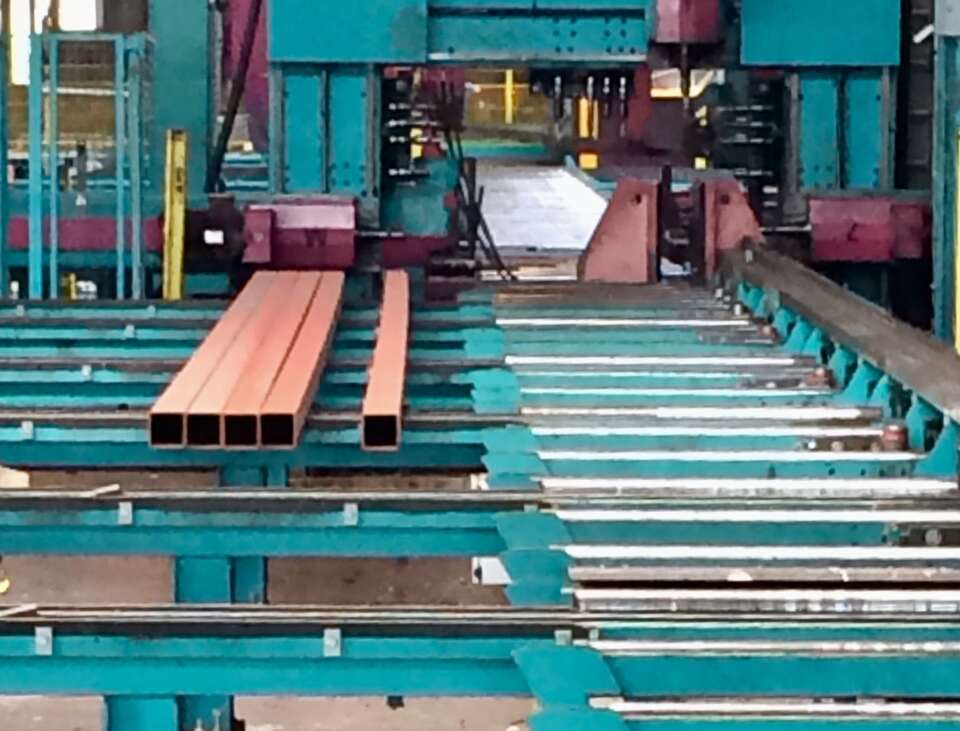
The disposal of trim cuts, finished parts and scrap can also be problematic. Beams with leaning flanges are incompletely grasped by the automatic discharge systems and often touch parts of the roller conveyors during transport. As a result, the automatic discharge system loses grip on the residual piece, which then falls out of the system and interrupts the automatic system. Such occurrences cause unplanned stops and therefore loss.
Finishing level of the starting material
Extreme burr formation, which occurs when sawing to length and/or cutting profiles in trade lengths, is an increasing source of irritation.
Clamps, magnets and gripper systems do not function as a result of these material deviations. These profiles cannot be processed on the automatic or even conventional processes without additional post-processing, or only with difficulty.
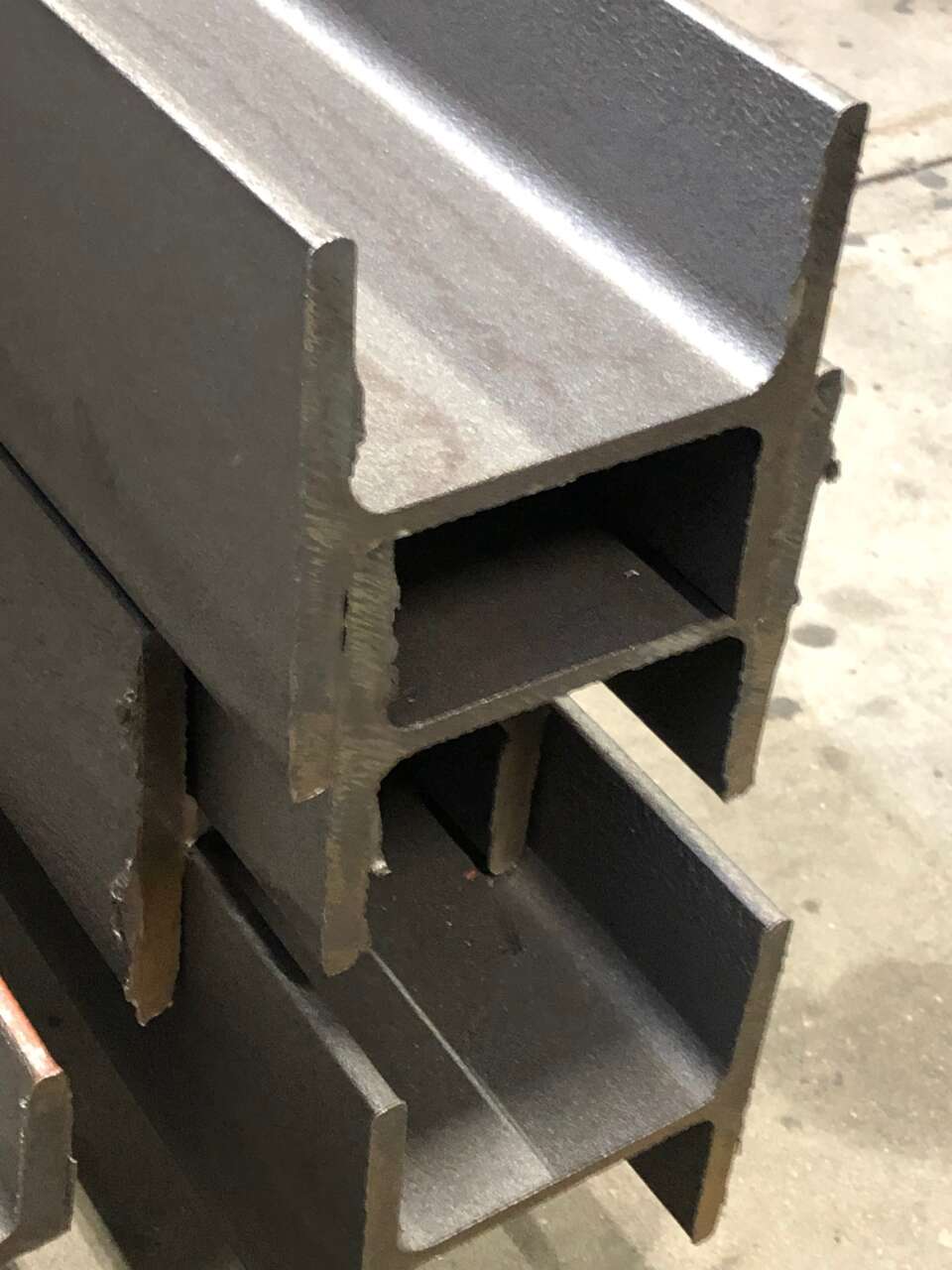
Finishing level of the basic / input material
Individual workflow vs. purchasing specifications - prevention is better than cure
In order to prevent malfunctions and downtime, it is advisable to take the existing machining processes, process specifications and automation into account when purchasing structural steel. The machining processes themselves are modular, the process design (the layout of roller conveyors and cross conveyors) and thus the workflow individual and specific to your internal process.
Knowledge of the possibilities and limitations of one's own process on the purchasing side prevents unnecessary disruptions in the production process in this case. Despite individual reference to standards for dimensional tolerances (e.g. EN-NEN 10034 / EN-NEN 10024) by both steel- and machine suppliers, it is recommended to discuss this at an early stage in the chain on the basis of the individual systems. After all, prevention is better than cure.
Prevention is better than cure
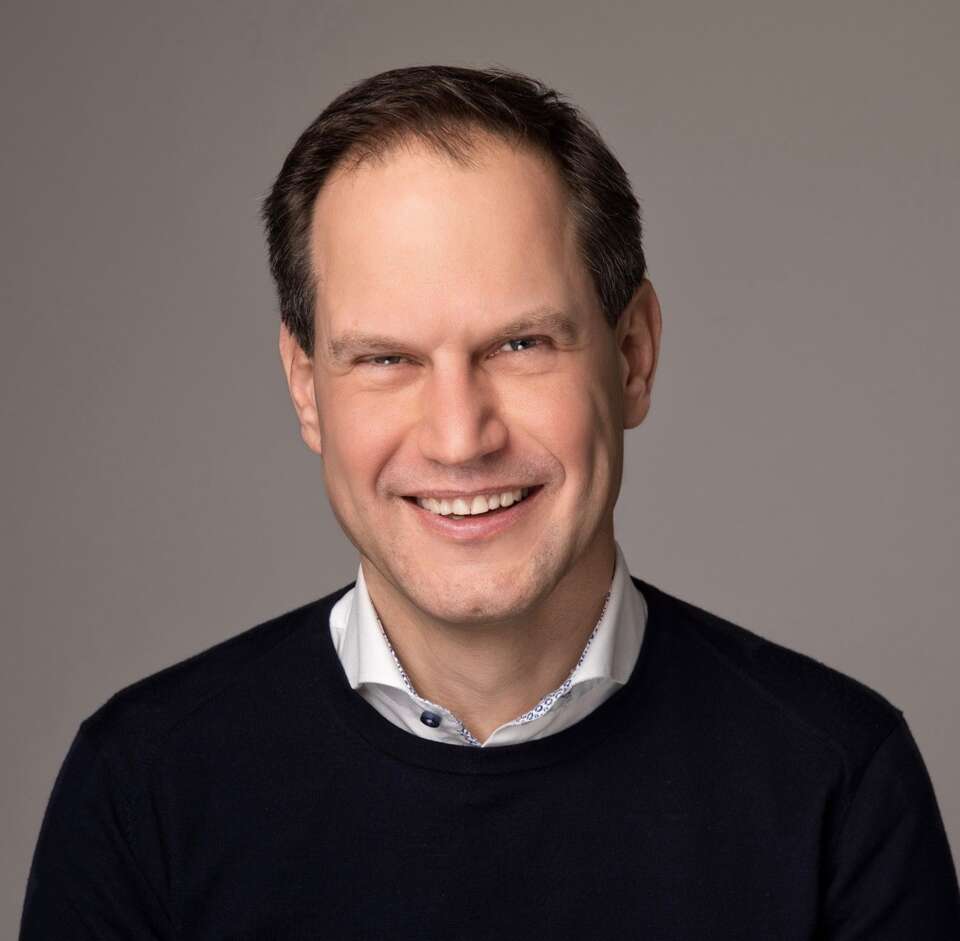