Do you recognize the situation below?
To the great frustration of your salesman, the customer has to be called again. The ordered items will not be delivered today as agreed, but tomorrow afternoon at the earliest. Incomprehensible to the salesman. In the system he had clearly seen that all materials were in stock. The material only had to be sawn, drilled and blasted and sprayed. For that he had counted on extra time... Heavily irritated, he goes to the production manager to tell his story. How is it possible that the delivery time is suddenly no longer met? Last week we sold more tonnage and everything was on time.
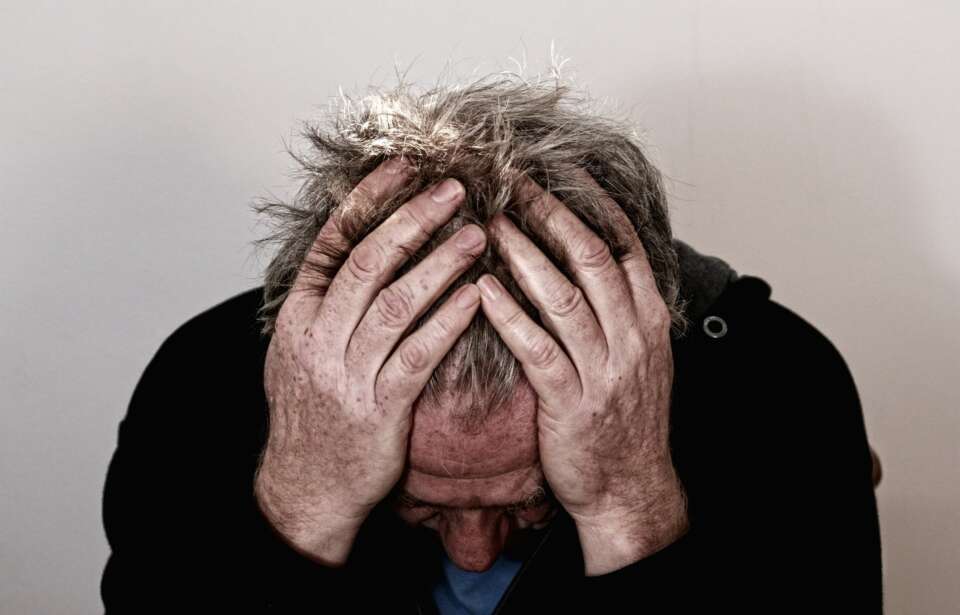
At the same time as the salesman, the director comes in irritated. He draws the production manager's attention to the fact that far fewer order lines are being picked this week than last year at this time. The production manager points out the large number of processing orders this week and the amount of handling related to, among other things, many saw cuts and drilling operations. Moreover, many of the processing orders sold can only be realized by pulling out all stops on the available machinery with questionable quality. In this way, high productivity is also impossible to achieve. Last week he was running at maximum capacity and all orders were picked just in time as well as all steel processing was completed just in time. To make matters worse, the drill is in breakdown for the second time this week. Precisely the machine on which most operations are planned. The production manager urging the maintenance manager to interrupt all work in progress immediately and rectify the fault instantly, otherwise no truck can be loaded at the end of the day and even customers with unprocessed trade lengths cannot be supplied.
This situation is clearly out of control.
The sales department is often unaware of the available steel processing capacity and the possible machining tolerances. Management is frequently focused on historical data analyses rather than future improvements. The maintenance department is often "blindfolded" because of tight short term control measures instead of long term improvement plans to improve the reliability and availability of the machining processes. Meanwhile, the production department is getting desperate and dictates therefore the maintenance department what to do. This behavior can also be described as a combination of "organized disorder" and "the circle of despair". Lack of common understanding of business processes and a forced highly reactive maintenance organisation. You need to understand the point from the installation maintenance and management perspective.
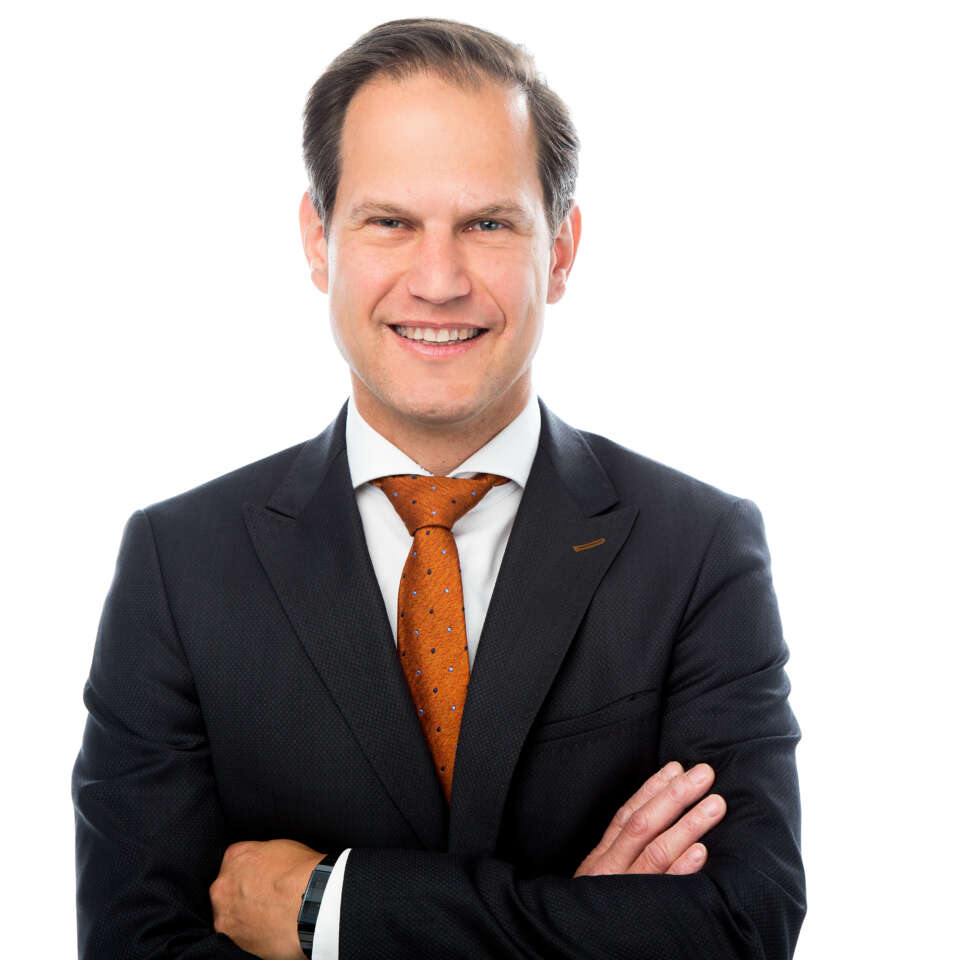
Want to know more?
Please get in touch with Ryan Ordelmans
Strong operational performance is achieved with reliable, available and productive steel processing. This requires organisation-wide involvement, a foundation, focus and adaptability and leads to low maintenance cost per ton. It is a culture - A way of life.