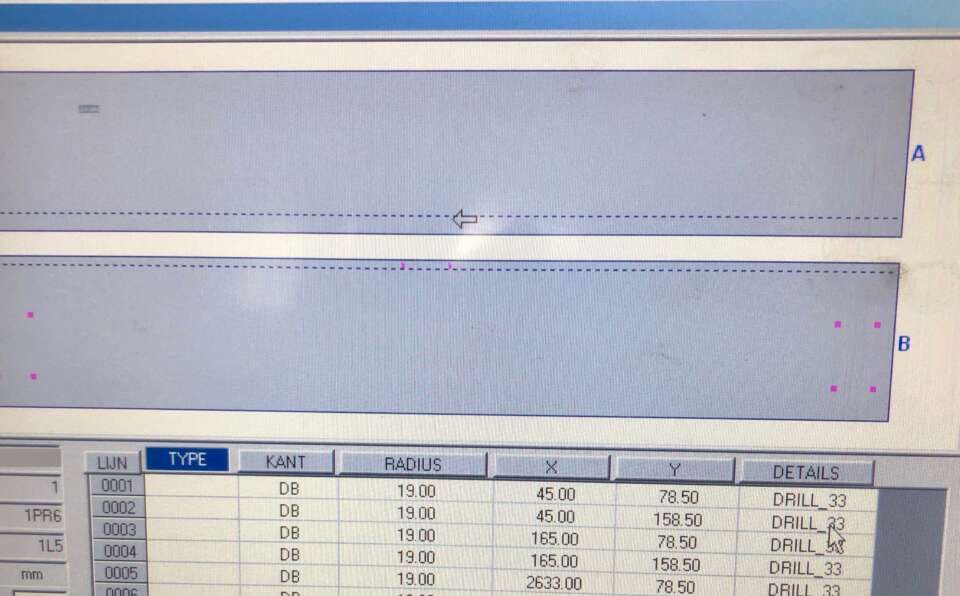
Optimisation with ERP and MRP software
Work that was previously carried out on the machine is now literally prepared by the work preparation department. With up-to-date ERP & MRP software solutions, it is possible to optimise and control machining operations. In addition to software knowledge, this also requires knowledge of the possibilities and limitations of fabrication machinery and workflows. What can and cannot be done on the machines? What needs to be changed in order to be able to process a certain material? Adjusting times between H-beams and angle profiles can take up to 30 minutes and drastically disrupt productivity. This knowledge is often not integrated in the MRP software and is also machine-specific. Often this knowledge is known to the machine operator, but not in the work preparation. Digitisation and automation can therefore lead to two machine operators, one on the process and one on the work preparation.
Are you prepared?
It is good to realise that digitisation and automation cause shifts in sub-processes and activities in these situations. Shifts of more than 10 hours a week from production to planning & work preparation are no exception. Good preparation prevents surprises and implementation problems.
More efficiency through insight
Good insight into and understanding of your production orders, (sub)processes and the individual activities form the basis for the next automation step. What adjustments and shifts are you prepared to make? To what extent does this have consequences for your organisation and can your organisation realise these adjustments? Do these adjustments outweigh the (predicted) savings as a result of an increased automation degree in the fabrication process? Is the practical knowledge of the fabrication machinery on the part of the operator and the work planner equal? Just a few questions that need to be asked beforehand. The answers to these questions and an additional process analysis provide the necessary insights for the right considerations and prevent surprises.
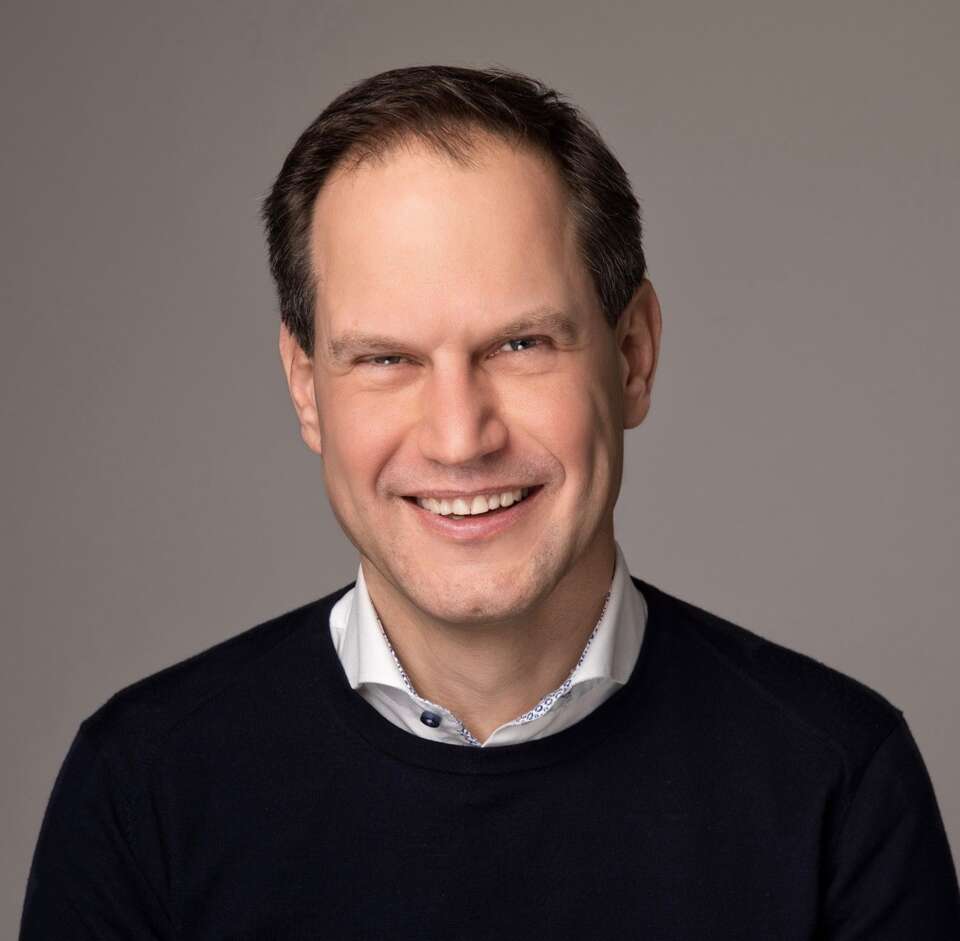