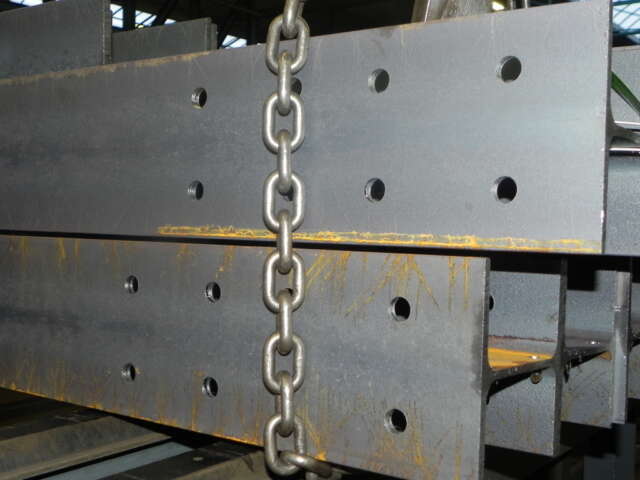
Why is that?
- Two people are often required to attach the load with chains.
- Attaching the load with chains is time-consuming and increases the risk of damage because the chain can get caught behind parts of roller conveyors and cross conveyors, causing damage and production downtime.
- Unstacking and spreading of bundles of material with chains is complex, takes time, is not without danger and requires the deployment of two people
- As a result of increasing automation and therefore CE measures, the loading and unloading zones of machining processes are protected by light barriers and fences. Loading and unloading of materials using chains as lifting equipment is only possible if automation and CE safety measures are interrupted and thus the process is (partially) stopped, which limits the productivity of the machines.
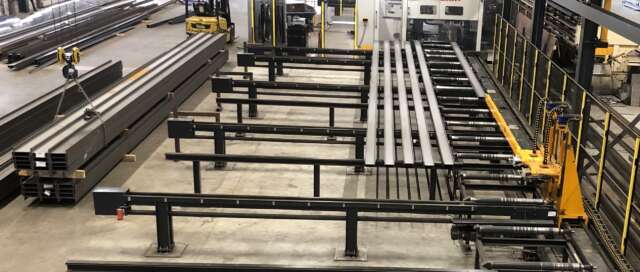
Result
The maximum capacity of the machining processes is not optimally used and the operational costs and stocks are too high. As a result, the total lead time is increased and thus the profit in the process is reduced.
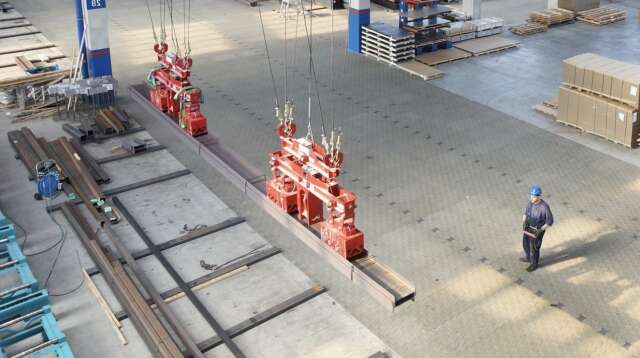
How can a magnetic crane contribute to a short throughput time, lower stocks and lower operational costs?
- When a magnetic crane is used, the manual attachment of the load with chains is redundant and the operation can be carried out by one person only / the machine operator.
- Picking up the material with a magnet is considerably faster and also protects the material and the transport system from damage, which increases the reliability and availability of the systems.
- Material unstacking and spreading is not only considerably faster, but also easier, safer and can furthermore be carried out by one person/machine operator
- Loading without interruption of the automation and safety systems is only possible with a magnetic crane, as this requires no manual intervention in the loading and unloading zones.
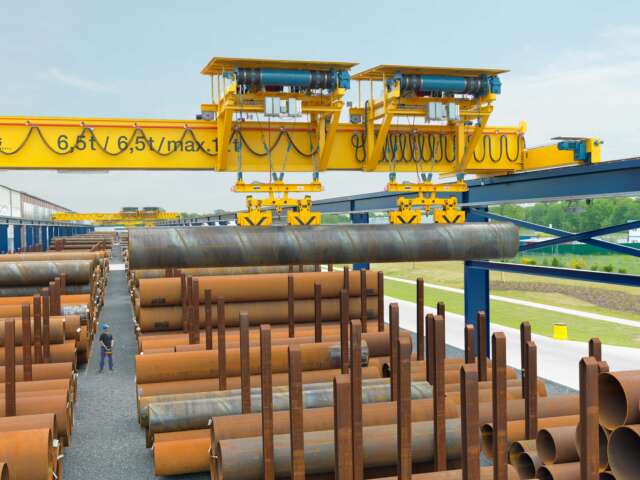
Preconditions:
- There is a difference between picking bundles of material from a storage area and laying them out and loading the processing machines. If the distances between the storage and processing machines are large, the use of two cranes is recommended. In that case often a magnetic crane for the machine operator and a crane with magnets and/or chains as lifting device for the logistical supply of bundles of material.
- A magnetic crane for loading processing machines only works well if a pendulum-free crane cable tension is used (often double cable tension). This limits load swing, even at considerably high travel speeds, while still ensuring maximum precision in positioning the load to and above the load.
- The hall must offer sufficient height for a hall crane with oscillation-free suspension of the magnets.
A bottleneck that does not need to be a bottleneck.
With increasing capacities, the importance of a seamless material flow to and from the processing machines increases. Faster machining processes with an ever-increasing degree of automation provide this effect. If you want to make optimal use of the maximum processing capacity of (modern) steel processing machines, loading and unloading by means of magnetic cranes is indispensable. It contributes to shorter throughput times, less stock and lower operational costs and therefore more cash flow!