- Neatness and cleanliness, process improvements as well as autonomous maintenance was achieved
- A new environment has been created where it’s also more pleasant to work
- Shotblasting, saw cutting and drilling is already considerably more efficient
- Surpex actually guided our own staff to implement these improvements themselves
“A clear report that we all support”
Quick Scan
IJzerleeuw wanted to create a sustainable, clean, well-organized, safe and efficient working environment, while avoiding defects, reducing search times and preventing accidents at work. “That’s exactly what Ryan Ordelmans at Surpex focused on,” says van Essen. “He started by visualising our status with a quick scan. I wasn’t the only person providing input, our work planner, the technical department, the logistics manager and of course operators were all questioned. This led to a clear report that we all support. Surpex then drew up an action plan to implement the proposed improvements at IJzerleeuw. This included paying attention to neatness and cleanliness around the machines, as well as process improvements and autonomousmaintenance.”
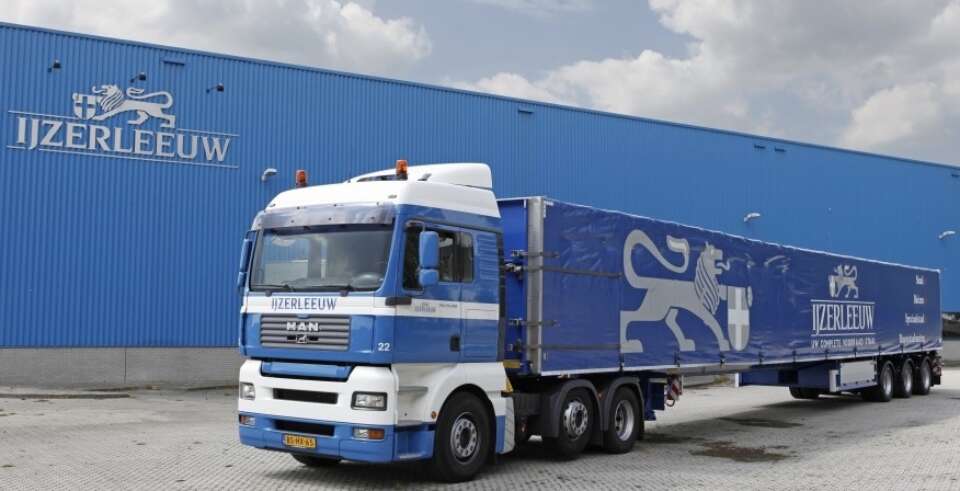
New Mindset
“Surpex implemented the improvements in very close collaboration with the seven people who work with our machines," says Johan van Essen. “That’s important because now that he collaborated with them on the improvements, our staff has a clearly changed mindset. People feel far more involved in the processes and machines and clearly take responsibility. Ryan Ordelmans, working with our staff, stressed neatness and cleanliness first. A 5S Lean Six Sigma method was implemented for each machine and a major maintenance run was carried out. Workstations and tool boards have been installed as well. This has created a new environment where it’s also more pleasant to work.”
“Essential machine documentation as well as process knowledge is now available at each treatment process in the form of one-point lessons”
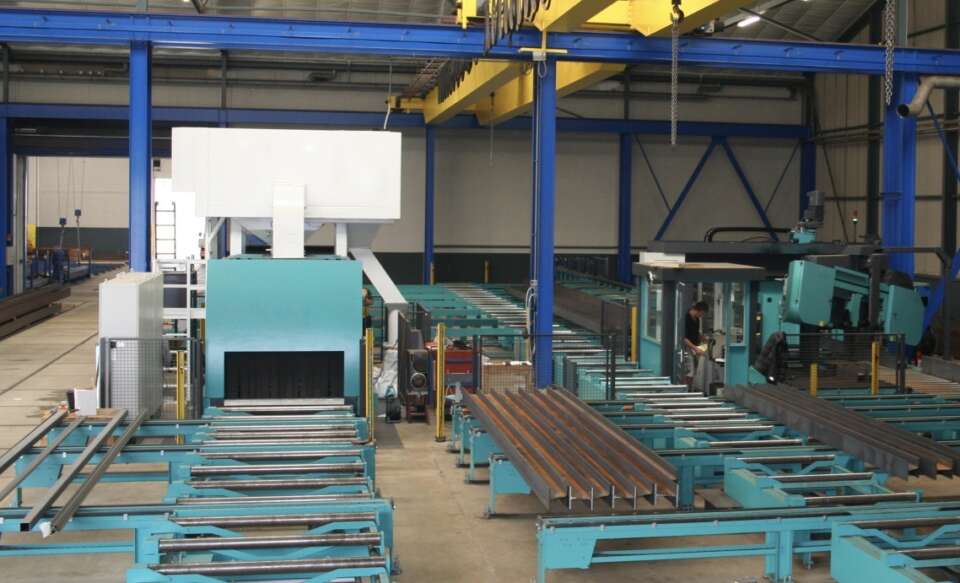
Process improvements & autonomous maintenance
Surpex subsequently proceeded with targeted process improvements as well as splitting maintenance in first, second and third-line maintenance. Van Essen: “Also, all available machine documentation was itemised including all available knowledge of the production processes. These are now available at each treatment process in the form of one-point lessons. In addition, together with Surpex, we introduced autonomous maintenance in seven steps which is secured by a periodic internal audit executed by ourselves. Surpex has supervised us during this process closely. The final result is that shotblasting, saw cutting and drilling is already considerably more efficient within our company. This will only improve over the next month when, following Surpex’ advice, we make a number of small changes to the machines that will allow us to be more flexible.”
“Voor ons is het belangrijk,” sluit Van Essen af, ”dat Surpex hier niet de procesverbetering zelf heeft doorgevoerd, maar feitelijk onze eigen mensen begeleid heeft om deze verbetering door te voeren. Daardoor hebben we een bestendig resultaat. Het proces is écht van onze mensen geworden. Die betrokkenheid zorgt voor een aanzienlijke kostenbesparing.”
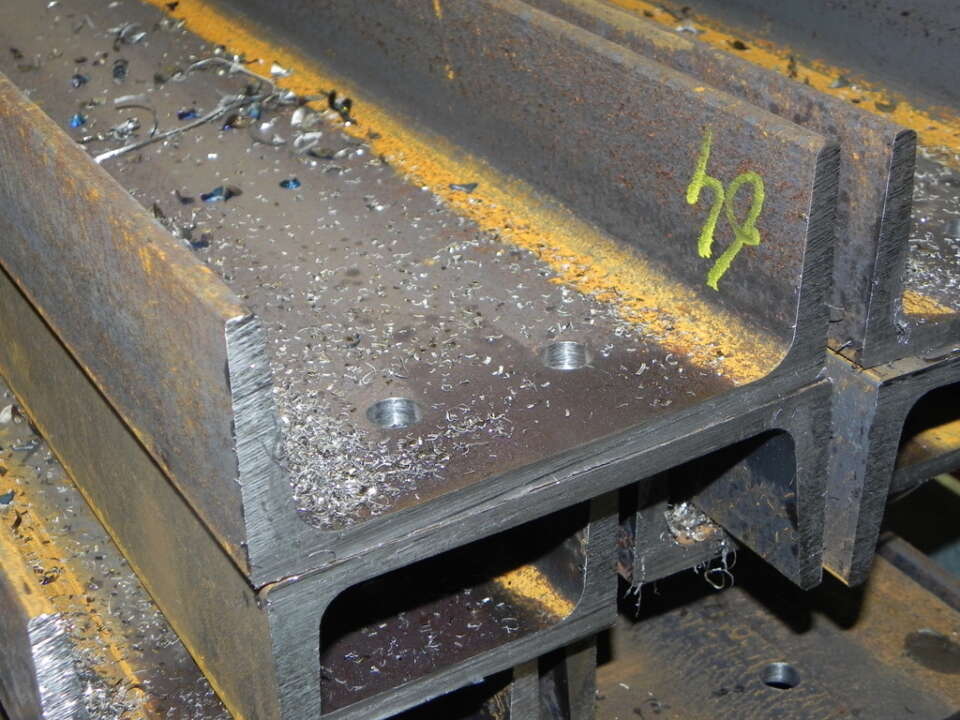