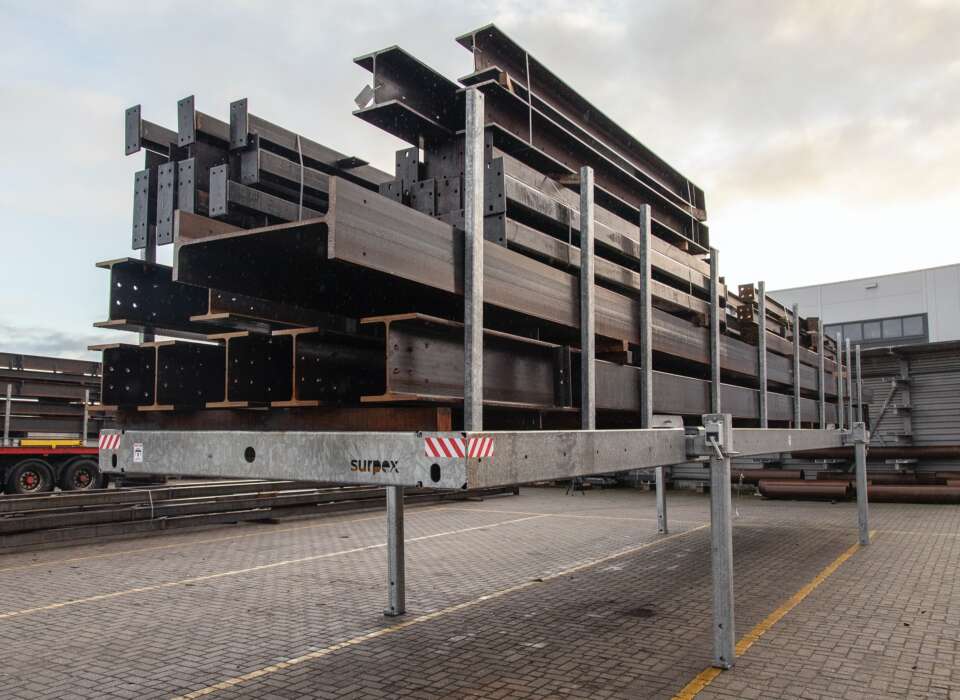
Key questions
- Which production strategy will enable us to achieve our corporate goals?
- How do we realise a factory layout that perfectly connects our production and logistics and guarantees flow in our production?
- How do we protect our production output and our risks when buying new production units?
- How do we achieve reliable, available and productive production?
- How do we manage our production units?
Strategies and solutions
Based on our in-depth knowledge, experience & expertise of your industry, branch and production machines, we work on realistic solutions in a down-to-earth, pragmatic and goal-oriented way. We switch effortlessly between management/office and shop floor. With our strong analysis and implementation skills, we support you and your team in implementing improvements in production and logistics.
- Manufacturing strategy:+−
A production strategy achieves the corporate goals and strategy by producing goods and thereby realising a lasting competitive advantage.
The ability of an organisation to excel in certain production functions compared to its competitors. A successful production strategy realises appropriate initiatives for this. Typical questions are:
- How are the production processes structured?
- Is the production facility suitable for realising the objectives?
- Which customer groups are served with which processes?
- What is a successful organisational setup of the production activities?
- Does the production facility have sufficient capacity to carry out all necessary pre-processing?
- How is expertise retained and transferred?
A hands-on analysis, advice and implementation approach including monitoring of progress.
- Factory & production layout+−
Maximum productivity is realised by efficiently and effectively converting production resources into results. Creating optimum production flow in both greenfield and redevelopment situations. A challenging process both at the level of production resources (machines, buildings, investments etc) and logistics. Especially when it comes to processing products with large dimensions. A reliable, available and effective production machine is not maximally productive if the logistical supply and outflow of ready products is not efficient. The combination of the right production activities (including production machines) and sophisticated logistics determine your result. A continuous challenge and a continuous need for reconsideration and adjustment. Ad hoc solutions are not a viable alternative. SURPEX helps organisations define and structure their ideal production system. Our extensive knowledge & experience in the steel construction, steel trading and mechanical engineering industries is our frame of reference. Internationally, we have seen the inside of hundreds of manufacturing companies and contributed to their technical production set-up.
- Investment, implementation and start-up+−
The customer pays for the work! Carefully planned inventory & procurement management and customised risk management during implementation and start-up phase ensures that unplanned downtime is avoided and that production is started up stably and on schedule. Surpex has years of experience with these processes and is familiar with the specific elements for stability and success.
- Establishment of inventory & purchasing team with clear priorities for planning, purchasing, production coordination, quality and maintenance.
- Analysis of and influence on own organisational structures and work processes caused by the target investment and implementation of the necessary changes
- Structured request for quotation (RFQ) processes. Clear expectation management between supplier and end user. Effective start-up management and guidance focused on market demand and production output,
- Early inventory of personnel requirements so that a stable quality level is available during implementation
- Reliable, available and productive production+−
Is your maintenance organisation a cost item or does it continuously add value to your business results?
Optimum process integration is a condition for reliable and highly available steel processing processes, both at an equipment and company level. This requires top-down participation and a targeted strategy in which logistics, maintenance (maintenance costs) and equipment management (investment costs) complement each other. The focus is on the entire and extended life cycle of machining processes and specifically on the factors that actually influence value creation:
- technical availability
- maintenance costs
- safety, health and quality
- investment expenditure
This is a process that does not take place automatically. Surpex assists and supports in the setting up and professionalising of departments for the implementation, operation/management and optimisation of steel processing processes. A reliable and available production process does not come about by chance. It requires a foundation, focus and adaptability – it is a way of life.
- Management and life cycle monitoring of production units+−
The market and technologies are developing rapidly. It is therefore advisable to critically monitor the lifespan of steel machining processes and to start up investment projects at the right time to maintain and strengthen the competitiveness of your equipment. These projects are not just about replacing technically outdated equipment, but also about modernising equipment that is functionally or economically outdated.
For proper management, is essential to keep an overview of all of your production units to be able to make well founded decisions. It is a continuous process. The process starts with providing insight into the life cycle of all individual equipment (long-term planning), in order to then monitor the lifespan of this equipment. Every year, a strategic analysis can be carried out of the equipment that needs to be replaced or modernised. For each of these pieces of equipment, it can be determined which end-of-life measure yields the highest value, so that the right project can be carried out. This results in an overview of projects to be carried out for which a budget must be made available and which must be realised and monitored. In addition, the life cycle plans must be updated based on the projects.
Even though his process sounds rather complex, this is in fact not the case. It can be realised in a step-by-step manner which provides surprising insights and also prevents unpleasant (financial) surprises. Thus, you gain control of competitive steel processing.
Surpex can help you achieve those goals – as an independent consultant or even as an interim project manager to steer everything in the right direction.
Referenties
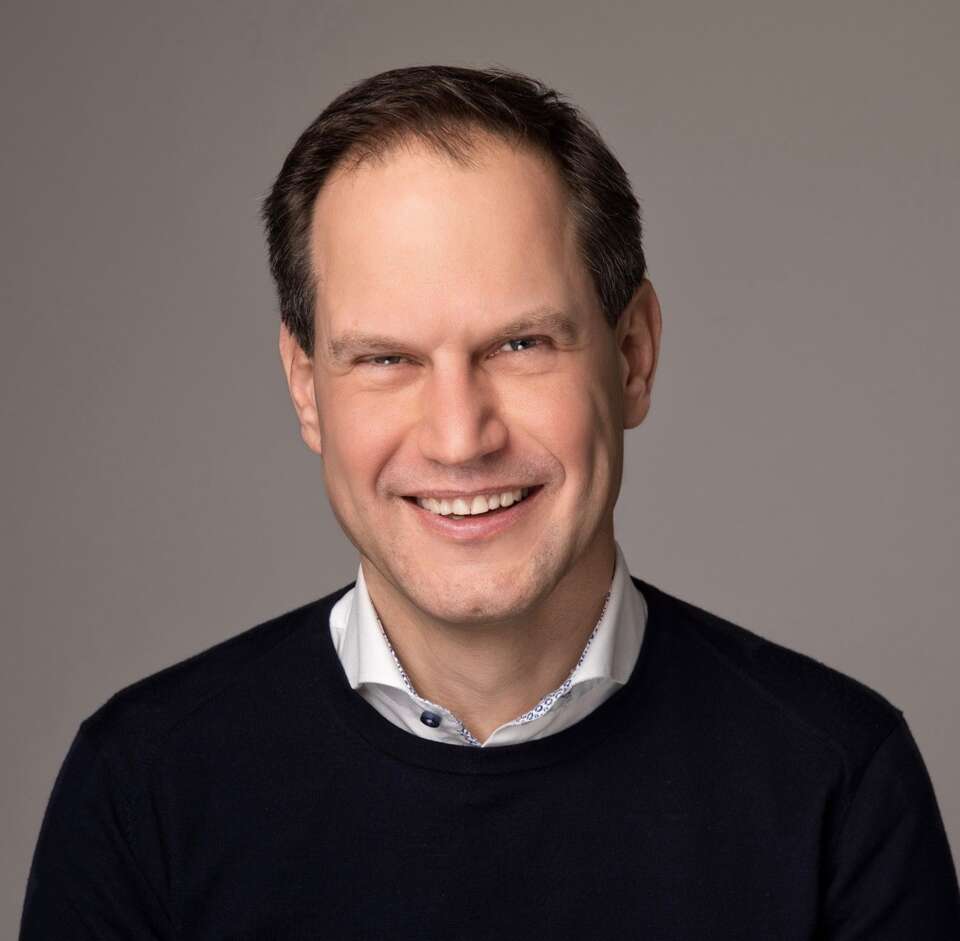